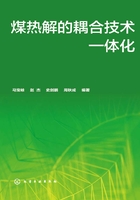
2.2 煤热解与半焦活化耦合一体化
煤热解与半焦活化耦合一体化的主要特点是:①将煤热解与半焦活化在同一立式炉内完成,可显著降低建设费用;②实现了一炉两用,可依据市场的需求,在不同时间生产不同的产品(半焦或活性半焦);③能进一步提高产物(焦油和煤气)的产率和经济效果。目前已实现工业化生产的技术是煤先热解-半焦后活化一体炉技术。
2.2.1 耦合一体炉技术
世界上最早利用煤炭生产碳基吸附-催化剂(活性半焦)的是德国。其最初开发了一种以硬煤为原料的专用活性炭基吸附-催化剂,命名为Activated Coke(活性半焦);其做法是将有相当细度的硬煤氧化处理后与黏合材料混合、成型,再通过炭化和活化后制成硬煤活性半焦。1987年7月,这种活性半焦被用于阿茨贝格(Arzberg)电厂5#、7#机组上(电功率分别为107MW和130MW)的联合脱硫脱硝装置中。1990年,又有1台安装了同样的联合脱硫脱硝装置的机组在Hoechst3-4电厂(电功率70MW)投入运行。后来为了进一步降低成本,又尝试以莱茵褐煤为原料生产出了褐煤活性半焦。这种由莱茵褐煤制造的褐煤活性半焦被莱茵褐煤公司(Rheinhraun)称为Herdofenkoks(HOK)。HOK采用一步法(Ⅰ-stage)制焦工艺,在这种工艺中,是将煤干燥、热解、内燃烧、加蒸汽活化完成的,并在波兰煤化工研究院作了进一步试验。其试验结果如表2-9所示。
表2-9 一步法的产品性能指标比较

北京国电富通科技发展有限责任公司已实现工业化生产的GF立式炉结构如图2-2所示。

图2-2 GF立式炉结构
GF立式炉采用外燃内热式气体热载体工艺,并实现炭化、活化连续运行。具体工艺流程:筛分后的褐煤经过输送带被送入煤斗,在重力作用下依次经过预热段、干燥段、干馏段、活化段和冷却段,最终活性半焦经刮板机排出炉外。在整个过程中,原料煤首先被来自冷却段的热烟气预热到80℃,脱除部分水分;然后进入干燥段被热烟气加热到170℃左右,脱除全部水分;干燥后的煤进入干馏段被热烟气与煤气的混合气体加热到800℃左右,脱除大部分挥发分;完成干馏后的半焦进入活化段,与高温蒸汽发生活化反应,形成发达的孔隙结构,成为活性半焦;最后进入冷却段,被来自干燥段的净化烟气冷却到100℃左右并排出炉外。在干燥段,出口烟气分成两部分,一部分作为配气重新被送入干燥段,用于调节干燥段热载体温度;另一部分经水洗净化后被送入冷却段吸收半焦中的热量。在干馏段,出口烟气分成三部分,一部分作为配气重新被送入干燥段,用于调节干燥段热载体温度;另两部分被分别送入干燥段和干馏段燃烧,提供所需热量。在活化段,出口水煤气经冷却后被送往锅炉燃烧。在冷却段,出口热烟气被送入预热段与原煤进行换热,实现半焦显热回收,提高GF立式炉热效率。
GF立式炉有以下主要特点:①干燥段与干馏段独立设计,避免干燥过程产生的大量废气和煤尘进入煤气净化系统,提高了煤气热值,降低了焦油中的含尘量;②采用多层布气方式,降低了气体阻力,热载体流量大,保证大处理量对热量的需求;③炭化、活化连续运行,减少了热量损失,提高了活性半焦炉的热效率;④采用废烟气作为冷却介质冷却产品活性半焦,避免了水资源浪费;⑤没有转动部件,内部构件全部国产化,投资低,运行可靠。
生产原料来自内蒙古大唐国际锡林浩特矿业有限公司胜利东二号露天煤矿褐煤,原煤和产品性质如表2-10所示,生产系统的物料衡算见表2-11。
表2-10 原煤和产品的工业分析(质量分数)

注:Mt——煤的全水分质量分数;Qnet,ar——收到基低位发热量。
表2-11 系统物料平衡表

生产实践表明,褐煤化学反应活性高,经过活化得到的活性半焦具有中孔发达、脱色能力强等特点。活性半焦由于灰分高,机械强度较差,对颗粒活性半焦的再生产生不利影响。经检测,其装填密度为654g/L,强度值为87%,比表面积和孔容积分别为673m2/L和0.84cm3/g,碘吸附值为325mg/g。
进行活性半焦吸附实验时,当吸附用水的COD为3106mg/L时,COD去除量为2183mg/L,单位活性半焦的吸附值为32.75mg/g,脱色效果明显。褐煤价格低廉,生产的活性半焦用于废水吸附处理可以降低成本,具有较好的市场应用前景。
杨湛明等在专利CN105776208A中,公布了一种活性焦的生产方法,该专利技术已于2018年在府谷县三联煤电化工有限公司实现工业化生产。
目前生产中炭化和活化分别在各自专用炉型中进行,而该发明将炭化(热解)和活化在兰炭(半焦)直立炉中同时进行,简化了工艺流程,避免了原料冷却再加热的过程,降低了能耗,更降低了活性半焦生产成本,并且使兰炭直立炉一炉多用,扩大了兰炭直立炉的适用范围;通过该发明方法制备的活性半焦比表面积大、吸附能力强,具有较发达的大、中孔结构,适合污水处理中去吸附对应的大、中颗粒污染物,所得活性半焦挥发分由兰炭时的约10%降低至3%以下,碘吸附值由兰炭时的100mg/g升到现在的450mg/g以上,脱硫值达到6.7~18.05mg/g。该产品活性半焦,在排污水提标治理中市场潜力非常大。
该发明采用粒度为3~15mm的长焰煤煤粉,相对于煤块来说,其价格低廉,成本较低。
在生产过程中,将形成兰炭过程中产生的荒煤气和形成活化产物产生的水煤气混合,经煤气净化系统后得到煤焦油和净化煤气,不仅回收了化工产品,而且回用净化煤气,节约了大量能源。
该发明的生产工艺过程如图2-3所示。

图2-3 活性半焦生产工艺过程
①将粒度为3~15mm的长焰煤装入兰炭直立炉顶部煤槽,然后经放煤旋塞和辅助煤箱送入兰炭直立炉;根据生产工艺要求,每半小时打开放煤旋塞向兰炭直立炉加煤一次。
②加入兰炭直立炉的原煤自上向下移动,与燃烧室送入兰炭直立炉的850~1000℃的高温气体逆向接触换热;兰炭直立炉的上部为预热段,中部为热解段,下部为活化段,煤在热解段被加热到750~850℃形成兰炭。
③兰炭继续向下移动进入高温蒸汽活化段,与输送至兰炭直立炉的850~1000℃的高温蒸汽反应,得到活化产物;步骤②形成兰炭过程中产生的荒煤气和步骤③形成活化产物产生的水煤气混合后经上升管、耐高温煤气伞以及桥管进入集气槽,送至煤气净化系统后得到煤焦油和净化煤气。
④将活化产物冷却,即得到活性半焦,冷却后的活性半焦由排焦装置排出,经带式输送机运出炉区产品库;所产活性半焦的碘吸附值为496~540mg/g,脱硫值为16.7~18.05mg/g。
净化煤气第一部分进入燃烧室与空气混合燃烧形成850~1000℃的高温气体;第二部分送入蒸汽锅炉与空气混合燃烧将水加热形成饱和蒸汽,饱和蒸汽经高温蒸汽加热炉换热后形成850~1000℃的高温蒸汽。高温蒸汽加热炉为两台,当其中一台通入饱和蒸汽时,另一台进行蓄热,且高温蒸汽加热炉利用第三部分净化煤气燃烧进行蓄热;两台高温蒸汽加热炉每2~3h循环交换一次,目的是把蒸汽锅炉产生的饱和蒸汽换热到850~1000℃的高温蒸汽,通过高温管道送进兰炭直立炉下部的高温蒸汽活化装置内,保证兰炭直立炉连续使用850~1000℃的高温蒸汽。
2.2.2 耦合一体炉结构
在专利CN205473585U中,对粉煤干馏活化一体炉的结构和操作过程作了描述。该一体炉的结构见图2-4。

图2-4

图2-4 粉煤干馏活化一体炉结构
1—料仓;2—插板阀;3—粉煤预热装置;4—热废气进气管道;5—煤气集气阵伞;6—探火孔;7—上水平气道;8—空废气预热道;9—上行富煤气烧嘴;10—立火道;11—下行富煤气烧嘴;12—下水平气道;13—高温蒸汽布气装置;14—上段定量排料阀;15—下段定量排料阀;16—刮板输料机;17—废气排出管;18—煤气集气罩;19—干馏段;20—蒸汽活化段;21—冷却段;22—上蓄热室;23—上行空废气交换器;24—废气管道;25—下蓄热室;26—下行空废气交换器;27—桥管;28—氨水喷淋装置;29—集气管;30—百叶窗砖;31—高温蒸汽管道;32—上行煤气进口管;33—下行煤气进口管
由图2-4(a)~(c)可见,一种粉煤干馏活化一体炉包括料仓1,料仓1的下部设有若干下料嘴,下料嘴下部连接有粉煤预热装置3,下料嘴与粉煤预热装置3之间设有插板阀2;粉煤预热装置3下部连接至炭化室,粉煤预热装置3与炭化室之间设有煤气集气装置,煤气集气装置包括设置在炭化室上部的煤气集气阵伞5;煤气集气阵伞5的底部连接有若干并列设置的煤气集气通道,所述煤气集气通道包括若干串联设置的煤气集气罩18,所述煤气集气罩18为圆台形;炭化室的内侧还设有用于将煤气输送至煤气集气阵伞5的百叶窗砖30;煤气集气阵伞5的出口端通过桥管27和集气管29连接至煤气净化系统,且桥管27和集气管29之间设有氨水喷淋装置28;炭化室的下部设有高温蒸汽布气装置13,高温蒸汽布气装置13的入口端连接至用于提供与粉煤反应的850~100℃高温蒸汽管道31;炭化室的底部设有活性半焦排料阀,活性半焦排料阀包括在竖直方向上平行设置的上段定量排料阀14和下段定量排料阀15,活性半焦排料阀的底部设有刮板输料机16;炭化室的两侧均设有用于将粉煤加热至750~800℃的粉煤加热装置,粉煤预热装置3的一侧连接有热废气进气管道4,另一侧连接有废气排出管17,且热废气进气管道4连接至粉煤加热装置。
粉煤加热装置包括上行加热装置和下行加热装置,所述上行加热装置包括上蓄热室22以及与上蓄热室22并列设置的若干空废气预热道8,上蓄热室22的上部设有连通空废气预热道8顶部的上水平气道7,上蓄热室22的下部连接有上行空废气交换器23;所述下行加热装置包括下蓄热室25以及与下蓄热室25并列设置的若干立火道10,所述立火道10与空废预热道8上下对应设置,且上下对应的立火道10与空废气预热道8连通,下蓄热室25的上部设有连通立火道10底部的下水平气道12,下蓄热室25的下部连接有下行空废气交换器26;上行空废气交换器23与下行空废气交换器26之间连接有废气管道24,所述废气管道与热废气进气管道4相连;立火道10的顶部设有能够将煤气从立火道10顶部通入的上行富煤气烧嘴9,所述上行富煤气烧嘴9连接至上行煤气进口管32,立火道10的底部设有能够将煤气从立火道10底部通入的下行富煤气烧嘴11,所述下行富煤气烧嘴11连接至下行煤气进口管33;上水平气道7的顶部设有用于对空废气预热道8与立火道10进行测温及检查的探火孔6。
该一体炉的操作过程是:由备煤单元运来的粒度0~25mm粉煤首先装入炉顶最上部的料仓1,然后打开插板阀2装入粉煤预热装置3进行预热脱水,煤在此段被加热到80~250℃左右;粉煤继续缓慢向下移动进入炉内干馏段19,煤通过此段被加热到750℃,并炭化成兰炭;热量来自煤气在立火道10内燃烧产生的废气,热量通过炉墙传递至炭化室中。750~800℃的高温兰炭继续向下移动进入蒸汽活化段20与高温蒸汽布气装置13出来的850~1000℃左右的高温蒸汽相遇,通过高温蒸汽管道31送进来的高温蒸汽,与高温兰炭进行化学反应。随着活化反应的进行,高温兰炭的碳原子不断与高温蒸汽反应,使得活化性半焦的产品堆积密度逐渐减小,同时产生比较多的微孔和中孔,因而产品碘吸附值≥650mg/g、强度≥96%;反应过程中产生的水煤气通过耐高温的煤气集气罩18及炭化室内侧的百叶窗砖30导出,进入煤气集气阵伞5,再进入桥管27,并通过氨水喷淋装置28降温除尘后进入集气管29,送到煤气净化系统回收煤焦油和净化煤气。产生的活性半焦由上段定量排料阀14及下段定量排料阀15同时经刮板输料机16输送到炉区产品库。
该一体炉采用上下交换加热的方式对炭化室中的粉煤进行加热,每小时循环交换加热一次。上蓄热室22和下蓄热室25均采用蓄热体,蓄热体为高铝耐火格子砖,以拓展燃烧室高温区域,提高上下整体加热均匀性。设置上蓄热室22和下蓄热室25的目的为回收废气热量,因此热效率较高,加热强度高。
当上部加热时,从煤气净化系统送过来的煤气由上行煤气进口管32从干馏炉的炭化侧上部送入炉内,经上行富煤气烧嘴9进入各立火道10;空气从上行空废气交换器23进入上蓄热室22,经上蓄热室22高铝耐火格子砖预热后,再通过上水平气道7进入各空废气预热道8预热炉墙,再进入立火道10;在立火道10上入口处,煤气与空气相遇燃烧。燃烧后的废气下行到下水平气道12汇集后,进入下蓄热室25与格子砖换热;然后经由下行空废气交换器26、废气管道24送到炉顶热废气进气管道4,进入粉煤预热装置3进行预热粉煤;预热后的废气经废气排出管17送到烟囱排入大气。
当下部加热时,从煤净化系统送过来的煤气由下行煤气进口管33从干馏炉的炭化侧下部送入炉内,经下行富煤气煤嘴11进入各立火道10;空气从下行空废气交换器26进入下蓄热室25,经下蓄热室25高铝耐火格子砖预热后,再通过下水平气道12进入立火道10;在立火道10下入口处,煤气与空气相遇燃烧。燃烧后的废气上行到空废气预热段8加热炉墙,再经过上水平气道7汇集后,进入上蓄热室22与格子砖换热;然后经由上行空废气交换器23、废气管道24送到炉顶热废气进气管道4,进入粉煤预热装置3进行预热粉煤;预热后的废气经废气排出管17送到烟囱排入大气。
粉煤干馏活化一体炉炉体由炭化室、燃烧室、蓄热室等组成,燃烧室包括空废气预热道和立火道。炭化室与燃烧室占据炉体一侧,炭化室沿炉体纵向贯通,其两侧为燃烧室。蓄热室占据炉体另一侧,沿炉体竖向分成两个蓄热室,一端分别与燃烧室相通,另一端与废气开闭器相连。炭化室为双排布置,采用净化后的煤气加热。