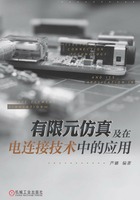
上QQ阅读APP看书,第一时间看更新
1.3.6 汽车连接器的抗冲击、振动、疲劳性设计
在汽车、航天连接器的可靠性设计要求中,抗冲击、振动、疲劳是非常重要的指标。以往传统方法,只有在物理样机完成后进行冲击、振动、疲劳实验,才能评估产品设计的可靠性,但在产品开发阶段很难实现。这种方法在产品的实效性上难以满足日益激烈的竞争需求。另外,对于需要长时间才能显现的疲劳问题,实验需要大量的时间,无法适应现代快节奏产品开发的需求。而建立产品的有限元模型,利用仿真技术进行连接器的抗振动、冲击、疲劳仿真分析,即可有效解决这一问题。
用仿真软件对汽车连接器进行模态、振动分析(见图1-38、图1-39),得到自振频率、振型、整体响应、每个振动模态下应力与位移参量。图1-40为连接器进行冲击仿真分析时加载的冲击载荷谱,图1-41为仿真得到的冲击载荷应力及变化曲线。由此可获得连接器的动态特性,为连接器的抗振、抗冲击设计提供依据。

图1-38 汽车连接器分析模型

图1-39 振型

图1-40 冲击载荷谱

图1-41 冲击载荷应力及变化曲线
长期动载荷作用引起的机械疲劳是导致连接器性能降低甚至失效的重要原因。利用仿真不仅能进行连接器应力、应变结构分析,还能用动力学仿真得到动态负载,在此基础上进而可以进行连接器的耐疲劳分析(durability)。如图1-42连接器的疲劳分析所示,图1-42a为疲劳损伤,连接器设计寿命与可用寿命的比值;图1-42b为连接器应力集中点,即最容易发生损伤处;图1-42c为安全系数,通过疲劳仿真可发现结构的薄弱位置,评估其安全性,并预测连接器的寿命。

图1-42 连接器的疲劳分析