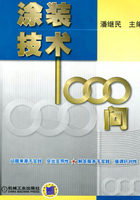
3.4 磷化
3.4.1 什么是磷化处理?
金属(主要指钢铁)经含有锌、锰、铬、铁等磷酸盐的溶液处理后,由于金属和溶液的界面上发生化学反应,生成主要为不溶或难溶于水的磷酸盐,使金属表面形成一层附着良好的保护膜,此过程称为磷化。
3.4.2 磷化处理有什么作用?
磷酸盐转化膜应用于铁、铝、锌、镉及其合金上,既可当做最终精饰层,也可作为其他覆盖层的中间层,其作用主要有以下方面。
(1)提高耐蚀性 磷化膜虽然薄,但由于它是一层非金属的不导电隔离层,能使金属工件表面的优良导体转变为不良导体,抑制金属工件表面微电池的形成,进而有效阻止涂膜的腐蚀。
(2)提高基体与涂层间或其他有机精饰层间的附着力 一方面,磷化膜与金属工件是一个结合紧密的整体结构。例如,锌系磷化,开始形成的是磷酸铁和黑色氧化铁,在其上再成长为磷酸锌,即在工件上直接生成磷化膜,其间没有明显界限。另一方面,磷化膜具有的多孔性,使涂料可以渗透到这些孔隙之中,涂料与磷化膜紧密结合,附着力提高。
(3)提供清洁表面 磷化膜只有在无油污和无锈层的金属工件表面才能生长,因此,经过磷化处理的金属工件,可以提供清洁、均匀、无油脂和无锈蚀的表面。
(4)改善材料的冷加工性能 如拉丝、拉管、挤压性能等。
(5)改进表面摩擦性能 以促进其滑动。
3.4.3 磷化膜怎样进行分类及其各自特征是什么?
可把磷化分为锌系、锌钙系、锌锰系、锰系、铁系、非晶相铁系六大类。各种磷化膜的分类及特点见表3-28。
表3-28 磷化膜分类及特点
3.4.4 磷化膜的分类、缩写符号及有关特征是什么?
磷化膜的分类、缩写符号及有关特征见表3-29。
表3-29 磷化膜的分类、缩写符号及有关特征
注:①为当基体为钢铁时的缩写符号,基体为其他金属时,缩写符号由供需双方协商决定。
②Me表示碱金属离子或NH4+。
3.4.5 磷化膜具有怎样的特性?
(1)多孔性 磷化膜具有多孔性的主要原因是磷化膜通常由许多大小相差悬殊的结晶组成,这些结晶从晶棱散布开来,然后连接在一起,逐步覆盖整个工件的磷化表面。磷化膜的空隙率由许多因素确定,一般占磷化表面积的0.5%~1.5%。一般磷化膜越厚,空隙率越低;结晶的细度越细密,空隙率越小;磷化膜质量增大,空隙率减少;但空隙率还与磷化膜的化学成分等有关系。
(2)膜重 磷化膜的厚度一般为1~50μm,对于涂装预处理的磷化膜膜重一般用每单位面积的质量来表示,单位为g/m2。膜重与磷化膜的用途有极大的关系,涂装前磷化膜的膜重要求小于10g/m2,一般在1~4g/m2。
(3)耐蚀性 磷化膜可为基体提供重要的防护作用,可防止腐蚀介质对金属工件的侵蚀。这是因为磷化膜具有不良导体性质,可以抑制金属工件表面微电池的形式,有效阻止腐蚀。但由于磷化膜是多孔的,所以单纯磷化膜的耐蚀性是有限的。
(4)与金属工件的结合力 磷化膜与金属工件的结合力,决定于磷化膜在晶界的生根情况,也取决于最佳定向结晶的百分数。
(5)与涂膜的结合力 磷化膜能为涂膜创造良好的底层,由于是多孔性的膜体表面,涂料可渗入其中,增加金属工件的表面积,同时涂料形成的涂膜和磷化膜可以相互渗透,提高涂层的结合力。
(6)绝缘性能 磷化膜是非金属涂层,是电的不良导体,它能使金属工件表面由优良导体转变为不良导体。
3.4.6 磷化处理的基本原理是什么?
磷化处理材料的主要组成为酸式磷酸盐,其分子式为Me(H2PO4)2,Me通常可以为锌、锰、铁等。这些酸式磷酸盐能溶于水,在含有氧化剂、催化剂的情况下,酸式磷酸盐的水溶液与洁净的金属表面相接触时,酸式磷酸盐分解,产生游离磷酸:
3Me(H2PO4)2=Me3(PO4)2+4H3PO4
游离磷酸把被磷化金属(以钢铁为例)表面的铁溶解下来,并放出氢气,这使金属与磷化液相接触的界面处酸度下降。
Fe+2H3PO4=Fe(H2PO4)2+H2↑
反应所释放出来的氢气被吸附在待磷化金属的表面上,从而阻止了磷化膜结晶的形成。为加速磷化反应的速度,使磷化处理时间短,以满足工业生产的要求,在磷化处理溶液内加有氧化剂与催化剂(又称去极化剂)以除去氢气。现以亚硝酸钠作催化剂为例,亚硝酸盐分解产生的NO2可使氢气氧化生成水,在钢铁表面(被磷化的工件)溶解下来的亚铁离子被NO2氧化成三价铁离子(FePO4),在磷化工作液的酸度下,它几乎完全不溶解,于是就成为淤渣沉淀下来。其反应式如下:
2Fe+2H2PO4-+2H++3NO2=2FePO4↓+3H2O+3NO↑
上述反应消耗氢离子,从而降低了酸度。在钢铁表面上氢离子的唯一来源是酸式磷酸盐,于是磷化膜就按下式沉积下来
3Me2++2H2PO4-=4H++Me3(PO4)2↓
将上述两个反应式结合起来,磷化过程的总反应方程式如下:
4Fe+3Me2++6H2PO4-+6NO2=4FePO4↓+Me3(PO4)2(磷化膜)+6H2O+6NO↑
实际的磷化反应远较上述复杂,因为有一些副反应生成。磷化淤渣的主要成分是FePO4,但其中也有少量的Me3(PO4)2。磷化膜的主要成分是Me3(PO4)2、H2O,但也有磷酸铁与黑色的氧化铁。在铁盐磷化过程中,由于所采用的酸式碱金属磷酸盐都是水溶性的,不能存在于磷化膜中。碱金属的磷酸二氢盐溶液在氧化剂的存在下,例如空气中的氧,与钢铁表面产生下列反应。
4Fe+4NaH2PO4+3O2=2FePO4↓+Fe2O3+2Na2HPO4+3H2O
3.4.7 磷化液的组成是什么?
磷化液由成膜物质、改性剂、促进剂、降渣剂及各种添加剂等组成,各自起着不同的作用。
(1)成膜物质 主要有磷酸、磷酸二氢锌和各种碱系磷酸盐和硝酸钙盐等,主要作用是:与铁反应生成磷化膜。
(2)改性剂 主要有可溶性的锌、锰、镍、钙盐,主要作用是:增加晶核,减少空隙,复合成型,提高耐蚀性等。
(3)促进剂 主要有硝酸盐、亚硝酸盐和过氧化物等,主要作用是:促进磷化膜生长,减少沉渣、改善外观等。
(4)降渣剂 有很多种材料可以起到降渣作用,主要有络合剂(如EDTA)、防垢剂(如聚丙烯酸)和缓蚀剂,其主要作用是吸附铁,使磷化膜结晶致密,提高质量。
(5)其他添加剂 如酒石酸可以降低膜重,提高药液稳定性;氨基多酸可以增加膜重;多磷酸盐可以降低膜重,节约药剂,减少沉渣。
3.4.8 常用磷化液配方及工作条件是什么?
常用磷化液配方及工作条件见表3-30。
表3-30 常用磷化液配方及工作条件
3.4.9 新型磷化溶液的发展趋势是什么?
磷化处理中,磷化液的组成和使用对磷化效果的影响较大。目前随着国内外环保形势的发展,新型磷化液的发展趋势如下:
(1)低温型磷化液 这类磷化溶液主要指磷化温度在35~55℃的低温磷化药剂和冬季也不需要加温的常温磷化药剂。
(2)低污染、低毒性 这类磷化溶液要求不含或少含亚硝酸盐和重金属盐类,尤其是既无亚硝酸盐又无镍的磷化溶液。
(3)长寿命、低成本 这类磷化溶液要求使用寿命长、单耗少,综合成本低。
(4)能满足新型涂装方式 这类磷化溶液要求能满足阴极电泳、静电喷涂等新型涂装需求。
(5)操作简便、管理简单 这类磷化溶液要求添加方便,所含组分少,管理容易。
在磷化处理中,已经很少单独使用单一金属盐的磷化液,常在金属表面形成复合型磷酸盐膜。在对金属工件表面进行磷化处理时,添加加速剂、调整pH值、时间的控制及表面封闭都是非常重要的。
3.4.10 磷化工艺流程是什么?
磷化处理一般工艺为:脱脂→热水洗→冷水洗→酸洗→冷水洗→磷化→冷水洗→钝化→冷水洗→去离子水洗→烘干。具体工艺流程的设定根据使用目的和磷化方法而不同见表3-31。
表3-31 磷化工艺流程
注:✔—需要;△—选用。
3.4.11 磷化处理有何要求?
1)为了获得质量更好更均匀致密的磷化膜,可以采用表面调整的方法,有轻度喷砂和抛丸等机械处理,酸洗和能产生表面吸附作用的表面调整剂。
2)由于磷化膜薄且多孔,耐蚀性有限,所以在磷化处理后,通常进行钝化,常用的方法是在空气中进行氧化,质量更好的方法是用铬酸盐进行浸泡处理。
3)磷化后水洗的目的是去掉磷化膜表面吸附的可溶性盐,防止涂膜起泡。注意要用干净的水进行多次冲洗,尤其是最后一道冲洗必须用去离子水。
4)水洗后干燥可尽快去除磷化膜中的结晶水,为下道涂装做好准备。最好采用烘干的方式,对于结构简单、要求不严的工件也可采用简单的自然干燥。
3.4.12 磷化操作方法有哪些?
1)磷化前工件表面的质量对磷化质量影响很大,要除掉油污、氧化皮、铁锈、残酸、残碱等,以免影响磷化膜的厚度和致密度,从而影响耐蚀性。因此,通常采用强酸强碱处理、喷砂、喷丸处理等方法使表面无油污、无锈蚀,表面状况良好。其中,喷砂、喷丸效果最好;采用强酸强碱处理,易使工件表面产生过腐蚀,因此要严格按工艺规程进行操作,以保证磷化质量。
2)根据磷化液的工作温度,分为低温磷化、中温磷化和高温磷化三种。操作前,根据选用的配方要求,将磷化槽和热水槽分别加热至工艺规定的温度。对磷化槽加热,不要采用直接加热方式,以免造成沉渣浮起,附在工件表面上,影响磷化质量。经过脱脂、除锈、中和、水洗后的工件,要及时移入磷化槽,入槽的速度应缓慢平稳。磷化时,磷化液应将工件完全浸没。按工艺规定达到浸渍时间后,将工件平稳地从槽中提起,移入热水槽中浸渍1min左右。热水槽的温度不宜低于80℃。待工件热透,用起重机将工件从槽中提出,待表面水分全部蒸发后,从起重机上卸下,用洁净的擦布和压缩空气把工件内腔和凹陷部位的积水清理干净,然后转入下道工序。浸渍磷化方法的优点是适用于处理形状复杂的工件,沉渣量少,设备维护容易。缺点是磷化时间较长,处理浓度高,膜层结晶粗糙。
3)喷射法一般在自动生产线上进行操作。被处理工件经过前道工序处理后,随输送线进入磷化喷射槽,这时应及时起动循环泵,对工件进行磷化处理。采用喷射法前要对配制的磷化液进行多次过滤,确保磷化液清洁无杂质和沉淀物。喷射时,调整好喷射压力,压力过小,容易使工件表面局部磷化不上;压力过大,磷化膜薄,较适宜的压力一般为0.05~0.15MPa。喷射的时间为1~2min。磷化后的工件可直接进入烘干室进行干燥处理。干燥温度为100℃,烘干时间为5~10min。然后,用毛刷刷掉表面浮灰,即可转入涂装工序。喷淋磷化方法的优点是适用于处理几何形状较为简单的板材,而且由于喷射时冲击力和磷化时化学作用的结合,使喷淋磷化的速度提高,浓度较低,膜层结晶较为细密、均匀。缺点是工件内部部位不易磷化,还易遭受腐蚀,喷淋的沉渣较多,设备投资大,维护困难。
4)刷涂法是直接将处理液通过手工刷涂的方式涂到工件上面,达到化学处理的目的。涂刷磷化方法的优点是适用于大型钢铁构件的磷化或局部磷化,能获得中等和较薄的磷化膜,设备投资少,磷化方便。缺点是磷化膜不够均匀,受人为因素影响较大。
3.4.13 浸渍磷化有何特点?
浸渍磷化处理按照工艺流程,将工件顺序浸入磷化液槽中进行处理。大型工件可用吊挂方式,小件用篮筐盛装。它是一种最早采用的磷化方式,目前应用最广。
浸渍磷化的优点是磷化槽液可以达到的地方均能进行处理,即适合于各种形状和结构的工件,设备维护工作量小,槽液浪费少,日常管理简单。其缺点是没有类似喷淋工艺机械冲刷的辅助作用,处理速度相对较慢,处理时间相对较长,特别是连续悬挂输送工件时,除了工件在槽中处理的时间外,还有工件空走时间、上槽下槽时间等,设备投资大,占地面积多,形成磷化膜结晶比较粗糙,磷化液浓度比较高。
3.4.14 喷淋磷化有何特点?
喷淋磷化是按工艺流程,将工件传递到处理位置,用泵将磷化液加压,并以0.1~0.2MPa的压力将磷化液形成雾状,喷淋在工件表面,从而达到磷化的一种处理方式。广泛用于家用电器、汽车处理等。
喷淋磷化的优点是具有喷射力冲刷和溶液更新作用,一般处理时间短,只需要1~2min,磷化膜结晶相对比较致密、膜薄,设备尺寸小,占地少,可以自动控制,槽液浓度较低。
其缺点是只适用于有油无锈的工件或几何形状简单的钣金件,对于几何形状复杂或有封闭内腔的工件,不易处理。设备维护量大,磷化液消耗较大,一般不适用有锈的工件。
3.4.15 涂刷磷化有何特点?
涂刷磷化是直接将磷化液(或多合一综合性处理液)通过手工刷涂在工件表面上,而达到磷化目的的一种处理方式,一般用在不宜采用浸渍处理或喷淋处理的大型钢铁构件或局部磷化,或没有磷化设备的厂家。设备投资极少,适应性强,操作方便,但对于不易涂刷的部位不适用,人为因素影响大,劳动强度大,易造成残液的加速腐蚀。
3.4.16 喷浸结合的磷化有何特点?
喷浸结合是将工件先喷淋,然后入槽浸渍,出槽后再喷淋,所有的浸渍喷淋均采用同一槽内的槽液。目前汽车车身的磷化已大部分采用这种方式。既保留了喷淋磷化速度快、时间短等优点,又保留了浸渍磷化对工件所有部位均可进行有效处理的优点。
3.4.17 怎样检验磷化处理的质量?
经过磷化处理的工件,磷化膜的质量检验应根据GB/T6807—2001《钢铁工件涂装磷化处理技术条件》,主要质量指标是三项:外观、磷化膜重、耐蚀性。
1.外观
磷化后的工件颜色应为浅灰色到灰黑色或彩色,膜层应结晶致密、连续和均匀。
磷化后的工件具有下列情况或其中之一时,均为允许缺陷:轻微的水迹、钝化痕迹、擦白及挂灰现象;在焊缝处无磷化膜;由于局部热处理、焊接以及表面加工状态的不同而造成颜色和结晶不均匀。
磷化后的工件具有下列情况之一时,均为不允许缺陷:有锈蚀或绿斑;疏松的磷化膜层;表面严重挂灰;局部无磷化膜(焊缝处除外)。
2.磷化膜的厚度
磷化膜的厚度分类见表3-32。
表3-32 磷化膜厚度(膜重)分类
3.耐蚀性
耐蚀性主要包括磷化膜的耐蚀性和磷化后涂漆漆膜的耐蚀性两部分。其检验方法如下所示:
(1)磷化膜耐蚀性检验 应将已降至室温的磷化试样浸入质量分数为3%的氯化钠水溶液中,并在15~25℃下,保持1h,取出试样,洗净、吹干,目视检查磷化表面不出现锈蚀(棱边、孔、角及焊缝处除外),则为合格。
(2)涂膜耐蚀性检验 将磷化后的工件喷涂厚度为25~35μm的白色氨基烘干磁漆涂膜试样,进行耐中性盐雾试验,铁系磷化膜的涂装试样经8h耐中性盐雾试验后,除划痕部位(指划痕任何一侧的附近宽度0.5mm范围内)外,涂膜应无起泡、脱落及锈蚀等现象则为合格。在涉及磷化膜质量检测中,还有一些其他相关的检验项目,如附着力试验、杯突试验、盐雾试验、硫酸铜试验、晶粒形貌与晶粒尺寸等。
1)附着力试验,应采用GB/T 9286—1998《色漆和清漆 漆膜的划格试验》和GB/T1720—1979《漆膜附着力测定法》进行。
2)杯突试验,应按照GB/T 9753—2007《色漆和清漆 杯突试验》进行。
3)盐雾试验,其方法应参照GB/T 1771—2007《色漆和清漆 耐中性盐雾性能的测定》和GB/T 10125—1997《人造气氛腐蚀试验 盐雾试验》进行。
在实际生产时,这些标准(附着力试验、杯突试验、盐雾试验、硫酸铜试验、晶粒形貌与晶粒尺寸等)可由供需双方协商确定。
3.4.18 常见的磷化质量问题及解决方法是什么?
常见的磷化质量问题及解决方法见表3-33。
表3-33 常见的磷化质量问题及解决方法
(续)
(续)
3.4.19 静电喷粉前磷化工艺是什么?
典型家用电器静电喷粉前磷化工艺见表3-34。
表3-34 典型家用电器静电喷粉前磷化工艺
(续)
3.4.20 混合散件磷化工艺是什么?
混合散件磷化工艺见表3-35。
表3-35 混合散件磷化工艺
3.4.21 电泳前磷化工艺是什么?
电泳前磷化工艺见表3-36。
表3-36 电泳前磷化工艺
3.4.22 什么是氧化?
通过氧化反应使金属表面产生保护性氧化膜的方法称氧化,经过氧化处理的工件可以大大提高金属的防锈能力,提高表面耐蚀性,是一种简单、廉价的金属保护方法。有化学氧化和电化学氧化两类。
钢铁材料的氧化,俗称发蓝,是通过化学或电化学的方法,在表面形成一层薄氧化膜(厚度一般为0.5~1.5μm)。根据工艺条件的不同(碱性、酸性、热氧化等),呈现不同的颜色,从蓝色至深黑色。
3.4.23 钢铁材料的氧化工艺是什么?
钢铁材料的氧化工艺见表3-37所示。
表3-37 钢铁材料的氧化工艺
注:1.1号氧化速度快,膜致密,光亮性较差。
2.2号含磷酸三钠,当铁含量多时,对氧化膜有增益作用。
3.3号为通用配方。
4.4号为二步法,第二步的药液浓度比第一步高,第一步完成后,直接进入第二步,氧化膜性能好。
钢铁经过氧化处理后,耐蚀性提高,但防护性仍然较差,需要进一步用铬盐、皂液、浸油等进行钝化处理,如果不进行涂装直接使用,需经常涂防锈油保持防锈状态。碱液法氧化工艺流程为:脱脂→水洗→酸洗→水洗→化学氧化→浸洗→水洗→钝化→水洗→吹干。不合格的氧化膜可以用浓度为100~150g/L的盐酸或硫酸溶液浸渍数秒即可清除,然后重新氧化。
3.4.24 钢铁材料表面氧化膜常见缺陷及处理方法是什么?
钢铁材料表面氧化膜常见缺陷及处理方法见表3-38。
表3-38 钢铁材料表面氧化膜常见缺陷及处理方法
3.4.25 什么是铜及铜合金的氧化?
铜及铜合金的氧化是指通过化学或电化学的方法在铜及其合金的表面形成一层薄氧化膜(厚度一般为0.5~2μm),其氧化膜颜色一般为黑色、蓝黑色。铜及铜合金化学氧化和电化学氧化工艺分别见表3-39和表3-40。
表3-39 铜及铜合金化学氧化工艺
表3-40 铜及铜合金电化学氧化工艺
铜及铜合金的氧化工艺流程为:脱脂→水洗→化学氧化(或电化学氧化)→浸洗→水洗→吹干。
铜及铜合金氧化操作时,要注意控制添加氧化液的浓度,浓度过低,膜生成不足,起不到防锈作用;浓度过高氧化膜则会溶化、脱落、疏松、结合力差。操作过程中要经常翻动,以保持氧化均匀。不合格的氧化膜可以用浓盐酸(质量分数为37%,全书同)或质量分数为10%硫酸溶液清洗掉,重新氧化。尽管经过氧化处理后生成的铜氧化膜比氧化铁致密性要高得多,但仍需涂油或涂料做进一步保护,以保持良好的防锈耐蚀状态。
3.4.26 什么是铝及铝合金的氧化?
铝及铝合金氧化指通过天然、化学或电化学的方法,在表面形成一层薄氧化膜(厚度一般为0.5~20μm),根据氧化液的不同,呈现从白色到彩色不同色彩的氧化膜。
铝及铝合金通过不同方法得到氧化膜质量的比较见表3-41。
表3-41 铝及铝合金通过不同方法得到氧化膜质量的比较
3.4.27 铝及铝合金化学氧化工艺是什么?
铝及铝合金化学氧化工艺见表3-42。
表3-42 铝及铝合金化学氧化工艺
(续)
3.4.28 铝及铝合金电化学氧化工艺是什么?
铝及铝合金电化学氧化工艺见表3-43。
表3-43 铝及铝合金电化学氧化工艺
注:配方1、3适用于一般要求的铝及其合金。配方2适用于高硬度、高耐磨铝及其合金。
铝及铝合金氧化处理的工艺流程为:抛光→脱脂→清洗→中和→清洗→化学氧化(或电化学氧化)→浸洗→水洗→吹干→烘烤→成品。
不合格的氧化膜可以用250g/L的磷酸溶液清洗掉,再次重新氧化。由于氧化铝的致密性比氧化铁要高得多,其防护性能也要好得多,铝及铝合金经氧化反应得到的氧化膜不需再进行涂装保护。
3.4.29 铝及铝合金氧化膜的常见缺陷及处理方法是什么?
铝及铝合金氧化处理时氧化膜和电化学氧化膜的缺陷及处理方法分别见表3-44和表3-45。
表3-44 铝及铝合金氧化时氧化膜的缺陷及处理方法
表3-45 铝及铝合金电化学氧化膜的缺陷及处理方法
氧化铝的致密性比氧化铁要高得多,其防护性能也要好得多,经反应得到的氧化膜不需要再进行涂装保护。
3.4.30 什么是钝化?
金属和铬酸盐作用生成三价和六价铬化层的过程称为钝化,也称铬化;一般用于铝、镁及其合金的处理,对钢铁也能形成铬化层,但很少单独使用。通常与磷化相结合,对磷化膜进行钝化处理,以封闭磷化膜中的空隙,进一步增强耐蚀性。
3.4.31 钢铁磷化膜的钝化有何特点?
钢铁磷化处理后再次钝化的主要作用是封闭孔隙,进一步提高其耐蚀性。钝化液规格是按照其含铬量的高低划分为中铬钝化、低铬钝化、超低铬钝化和无铬钝化。
1)中铬钝化能褪除磷化膜上的粉状物,质量好,但存在含铬量大,废水难于处理等问题,目前已较少使用。
2)低铬钝化含铬量为2~5g/L,钝化液稳定,钝化时间短,操作简单,钝化质量好,但含铬量仍然偏高,废水处理费用偏高,应用较少。
3)超低铬钝化,含铬量0.0125~0.05g/L,具有钝化液稳定、钝化速度快、含铬量低、使用成本较低的优点,且兼具含铬钝化的优点,是目前应用最为广泛的方法。
4)无铬钝化可分为有机聚合物钝化和无机钝化,其中比较成功并批量生产使用的是以六氟化锆为主要成分的钝化液,还有钛盐钝化液、钼酸盐钝化液、亚锡盐钝化液等,从总体性能上看,还未完全达到含铬钝化液的水平,其应用还不太广泛。常用的钢铁磷化膜的钝化液配方见表3-46。
表3-46 常用的钢铁磷化膜的钝化液配方
3.4.32 铜及铜合金的钝化有何特点?
铜及铜合金表面钝化的工艺流程为:脱脂→热水洗→冷水洗→酸洗(浓盐酸或质量分数为10%的H2SO4,室温30s)→水洗→强酸洗(H2SO4与HNO3体积比为1∶1,每升加入1.5gNaCl,室温3~5s)→水洗→表调(30~90g/LCrO3,15~30g/LH2SO4,15~30s)→水洗→酸洗(质量分数为10%的H2SO4)→水洗→钝化→水洗→烘干。铜及铜合金钝化处理时不合格的钝化膜可采用热的质量分数为10%的H2SO4溶液、浓盐酸或300g/L的氢氧化钠溶液浸泡去除。铜及铜合金的钝化液配方见表3-47。
表3-47 铜及铜合金的钝化液配方
3.4.33 铝、镁及其合金的钝化有何特点?
铝、镁及其合金的钝化即用铬酸盐进行的酸性氧化。铝、镁及其合金钝化处理时的工艺配方见表3-48。
表3-48 铝、镁及其合金钝化处理时的工艺配方