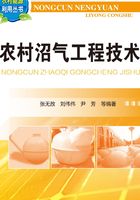
第十节 沼气发酵器的类型
一、常规消化器
常规消化器(conventional digester)也称常规沼气池,其结构简单,应用广泛。消化器内原料可分为四层:浮渣层、上清液层、活性层和沉渣层(图1-34)。发酵温度为常温,有机负荷为1~2kg/(m3·d),产气率为0.2~0.5m3/(m3·d)。我国的水压式沼气池、曲流布料沼气池、浮罩式沼气池以及印度的哥巴式沼气池均属这类消化器(图1-35)。

图1-34 常规沼气池料液结构分布

图1-35

图1-35 常规消化器
二、高速消化器
高速消化器(high rate digester)是世界上使用最多、适用范围最广的一种消化器。由于高速消化器内设有搅拌装置,使发酵原料与微生物菌群处于完全混合状态,活性区遍布整个消化器,消化效率高(图1-36)。高速消化器多采用恒温连续投料或半连续投料工艺,发酵温度属中温或高温,滞留期一般超过15d,有机负荷率为中温3~4kg/(m3·d),高温5~6kg/(m3·d)。

图1-36 高速消化器
三、厌氧接触消化器
厌氧接触消化器(anaerobic contact digester)采用污泥沉淀槽,使活性污泥回流进入消化器,将固体滞留期(SRT)与水力滞留期(HRT)加以区分,以此增加消化器内固体物的滞留时间及活性污泥的浓度,同时减少出料中的固体物,使该工艺具有较高的有机负荷和处理效率,产气多且稳定(图1-37)。我国南阳酒精厂就是采用此工艺的,发酵温度为52~54℃时,消化器负荷为9~11kgCOD/(m3·d),滞留时间为4~5d,COD去除率达82.2%~83%,池容产气率为4~5m3/(m3·d),每立方米废醪可产沼气22.6m3。

图1-37 厌氧接触消化器
四、厌氧滤器
厌氧滤器(anaerobic filter,AF)内填充有介质,厌氧菌群可附生在介质的表面并形成生物膜(图1-38)。处理污水时,有机物被分解利用,而微生物附着生长不易流失。一般细菌从生成到生物膜脱离需要150~600d,这样大大提高了消化器的处理效率。其优点为增加物料和菌种的接触机会,缩短物料的滞留时间;其缺点是在过滤中容易被大量生长的微生物堵塞。常用的介质有石头、煤渣、聚四氟乙烯、聚丙烯、聚乙烯等。

图1-38 厌氧滤器
近年来,在厌氧滤器中多采用各种形状的硬质塑料制品或软性合成纤维作为填料。维里尔(Verrier)的实验结果表明,各种合成材料的疏水性对于产甲烷菌的黏附和厌氧生物膜初始发育速度有直接影响,疏水性表面如聚四氟乙烯(PTFE)、聚丙烯(PP)、聚乙烯(PE)有利于疏水性细菌如甲烷毛发菌的黏附。相反,马氏甲烷八叠球菌则不直接黏附。在连续培养中,疏水表面即PP和PE的菌落形成要比较为亲水的表面如聚氯乙烯(PVC)和聚缩醛(PAC)的菌落形成快得多(表1-56)。
表1-56 不同材料表面产甲烷菌的附着情况(每100mm2平均值)

中国科学院广州能源研究所利用分段部分填充厌氧滤器处理糖蜜酒精废液,发酵器体积130m3,有机负荷为16.6kgCOD/(m3·d),进料COD含量为34060mg/L,HRT为2.5d,发酵温度32℃,去除率达81.1%。
五、升流式厌氧污泥床
升流式厌氧污泥床(upflow anaerobic sludge bed,UASB)1977年由Lettinga等研制而成,消化器上部安装有气、固、液三项分离器(图1-39)。在该消化器内,所产生的沼气在分离器下被收集起来,污泥和污水升流进入沉淀区,由于该区不再有气泡上升的搅拌作用,悬浮于污水中的污泥则发生絮凝和沉降,它们沿分离器斜壁滑回消化器内,使消化器内积累起大量活性污泥。在消化器底部是浓度很高并具有良好沉降性能的絮凝颗粒或颗粒状活性污泥,形成污泥床。有机污水从反应器底部进入污泥床并与活性污泥混合,污泥中的微生物分解有机物生成沼气,沼气以小气泡形式不断放出,在上升过程中逐渐合并成大的气泡。由于气泡上升的搅动作用,使消化器上部的污泥呈悬浮状态,形成逐渐稀薄的污泥悬浮层。有机污水自下而上经三相分离器后从上部溢流排出。

图1-39 升流式厌氧污泥床
在升流式厌氧污泥床内,颗粒污泥的形成是厌氧消化过程的一个新发现,它实际上是沼气发酵微生物的天然固定化。颗粒污泥具有较强的产甲烷活性和良好的沉降性能,对消化器负荷的提高和运转的稳定性均有显著作用。但活性污泥层形成的时间较长,一般要三个月以上才能逐渐达到正常运行的要求。
六、厌氧床工艺
这一工艺分为厌氧膨胀床(anaerobic expended bed)和厌氧流化床(anaerobic fluidized bed)两种,目前多为实验室装置。厌氧膨胀床和厌氧流化床同属于附着生长型生物膜消化器,在其内部填有像沙粒一样大小的惰性介质,如焦炭粉、硅藻土、粉煤灰或合成材料等,颗粒直径一般为0.2mm左右。有机污水在介质空隙中自下而上穿流而过,污水及所产沼气的上升速度足以使惰性介质颗粒呈膨胀状态或流态化(图1-40)。每一个介质颗粒都被生物膜所覆盖,这样使每单位体积消化器可以比悬浮生长或厌氧滤器工艺具有更大的有效表面积,能够支持更多的生物量,从而提高厌氧生物降解能力。

图1-40 厌氧膨胀床消化器
七、两相厌氧消化器(two phase anaerobic digester)
该消化装置又称两步发酵器,即把水解酸化与产甲烷阶段分离置于两个消化器内(图1-41),适用于处理多种固体废弃物,解决了固体原料发酵酸化和出料难的问题。

图1-41 两相厌氧消化器
八、干发酵
干发酵(dry fermentation)工艺是指发酵原料的浓度在20%~30%的沼气发酵工艺,一般采用批量方式进料,浓度以20%左右为宜,超过30%则产气量明显下降。该工艺要求接种量大,通常为1/3~1/2,每次可持续较高产气率2~3个月。在我国农村实际采用的干发酵装置有以下几种。
(1)干稀配套池 即修建一个水压式沼气池和一个干发酵沼气池,干发酵池容一般为3m3,主要用于处理秸秆,水压池主要用于处理粪便,并提供干发酵池的启动用接种物。这种形式又称为小双池或粪草分离池(图1-42)。

图1-42 干稀发酵配套池
(2)“大开口”干发酵池 这类沼气池的主要特点是开口很大,便于进料和出料(图1-43)。开口采用红泥塑料来密闭并解决其贮气问题,不再另设贮气箱,此类干发酵可以吸收部分太阳能以提高池温。在北方春、冬季节改作它用,如贮存物品,加塑料大棚后种植蔬菜。

图1-43 大开口干发酵池
(3)工厂化薄铁皮干发酵池 用薄铁皮铁罐式沼气池,容积一般为1.5~2.0m3,运输和移动非常方便。采用高压贮气,不需另设气箱,其承受压力可达1.5个大气压。该沼气池应放于背风的地方,在晴朗天气,其池内温度可达30℃以上,发酵周期为20d,池容产气率大于0.8m3/(m3·d)。出料时可利用池内沼气压力,一次可自动冲出2/3的发酵料液。
(4)利用水压式沼气池进行干发酵 其主要方法是根据发酵时间控制加水或出水量。可以先干发酵再转为一般湿发酵,或先进行湿发酵逐渐转为干发酵。
干发酵的特点如下。
①干发酵的池容产气率较高,是目前我国农村条件下解决沼气发酵产气率低的有效途径之一。此外,采用干发酵工艺可缩小沼气池的体积,方便进出料,节省劳力。该工艺尤其适合于我国北方习惯施用固体肥料的农村和较干旱的地区。
②干发酵的原料利用率不算太高,但从能源、肥料等综合效益来看是可行的。农村家用沼气干发酵的TS浓度以25%~30%为宜。这样的干发酵,原料利用率与农村目前使用的水压式沼气池发酵相当。
③沼气干发酵工艺技术的关键是在较高的TVA含量水平上发酵运转的pH控制问题。除沼气发酵的一般条件之外,合理的原料配比、适当的原料预处理和较大的接种用量是保证干发酵正常启动的三条主要措施。
九、塞流式厌氧消化装置
塞流式厌氧消化装置(plug-flow anaerobic digester)是两相厌氧消化和常规发酵结合的一种工艺,但该池不像两相厌氧消化那样严格分开,投料后采用逐渐推进流动,故而称塞流(图1-44)。这种沼气池结构简单,投资少,对各类粪便均有较好的产气效果,投料浓度可高达10%~13%;若加搅拌装置,可提高产气量15%~20%。

图1-44 塞流式厌氧消化装置
十、管道厌氧消化器
管道厌氧消化器(pipeline-type anaerobic digester)的研究试图使维持保留较高浓度的活性污泥、两步厌氧消化和塞流式运行等性能兼备于同一厌氧消化系统中,以获得较高的效率,同时节省运行的动力和简便操作管理。
这种工艺的反应装置的设计思路为:管道形式的装置符合化工反应设备的发展趋势,且便于设置于地下,既可为应用单位在建立废水处理设施时提供一条解决土地紧缺的途径,又可降低反应温度受气温影响的程度;因其横向水平敷设,有利于节省水力运行的动力,便于管理人员观测和操作;管道内充以供微生物附着生长的介质,可以持留较高浓度的活性污泥。管道系统分管节填充介质和横向串联,不仅便于加工制作及安装维修,还可以削弱消化液纵向返混,有利于呈塞流态运行和形成两步厌氧消化;而且当受超负荷冲击等不利因素干扰时,可将厌氧消化不平衡的状况限于局部,避免扩散到全系统,便于及时控制纠正,管理较简便。
此工艺先后通过处理几种废水的实验,和453m3容积的装置处理柠檬酸废水试生产性运行,验证了其原始设计构思的可行性与可取性,达到了研究的预期要求。至今,这项技术已在国内推广、转让给四省、一市的十余个单位。现将这一工艺有关研究的结果综述于下。
现以此工艺试生产性处理柠檬酸废水为例,介绍其流程与反应装置。杭州柠檬酸厂废水COD浓度的变幅为12~20g/L,pH为4.0~4.6,温度60℃上下。选用25~33℃中温条件;进水的pH值在启动期间应当调节,启动后不加调节。工艺流程见图1-45所示。

图1-45 管道厌氧消化工艺流程图
1—废水高位贮槽;2—玻璃钢冷却塔;3—提升泵;4—转子流量计;5—管道厌氧消化器的管节之一;6—水封;7—集水沉池;8—气水分离装置;9—气体流量计;10—浮罩式气柜;11—阻火器
试生产性反应装置原设计由7个直径1.2m、长6m的管节(图1-46)连成,总容积45m3,实际运行试验的结果表明,为兼顾运行的效率与出水的水质,可取4或5个管节组成。各管节充以外径6~8cm的空芯球状填料,前、后端分别设进、溢料管口,另设有气室(兼作人孔)、视镜、过剩污泥排放口。各管节的气室用导气管并联。

图1-46 组成45m3总容积反应器的单一管节示意图
随着厌氧消化工艺研究的深入,有关工程技术正向高效、稳态、低投资、低能耗的方向发展。管道厌氧消化工艺兼赋持留高浓度活性污泥、塞流式运行和两步厌氧消化等有利于提高厌氧消化效率的性能于同一反应装置中,有效地提高了容积效应;横向的管道形式便于设置地下,为用地紧缺单位提供了解决地皮困难的一条途径,还可以节省运行的动力能耗;对反应装置的运作有一种独到的检控技术,使管理简便,效率稳定。所有这些均符合当前国际厌氧消化技术发展的趋势,构成了此工艺的特色与优势。
国外曾报道过卧式塞流消化器或管道(隧道式)消化器(Tubular Digester或Tunnel Digester,Fry,1950,1974),虽然其名称上同此工艺的管道厌氧消化器相似,但前者仍属效率较低的常规厌氧消化器,在装置的结构、性能、运行性状及效用上与后者有本质的差别。